Luistiventtiilit, teollisen vallankumouksen tuote, have long held a dominant position in the industry despite the historical presence of many other valves such as globe valves and plug valves. kuitenkin, in recent years, gate valves have faced increased competition from ball valves and butterfly valves, which have captured more market share.
Unlike Palloventtiilit, tulppaventtiilit, ja läppäventtiilit, luistiventtiilit have a unique closing mechanism. The closure element, gate or disc, moves linearly by multiple rotations of the stem or spindle. It ascends from the pathway and enters the valve top (called the bonnet). Nämä venttiilit, opening linearly, are also known as multi-turn or linear valves, differing from the quarter-turn valves where the stem rotates 90 astetta, usually without ascending.
Gate valves come in various materials and pressure ratings, with sizes ranging from as small as NPS ½ inch to as large as NPS 144 tuumaa, catering to a wide spectrum of applications. The predominant design for gate valves consists of components manufactured through casting, taonta, or welding, with casting design being the dominant one.
One notable aspect of gate valves is their ability to fully open, providing almost no obstruction or friction to the flow path. The flow resistance offered by fully opened gate valves is roughly equivalent to a section of pipeline with the same port size. Consequently, gate valves are still widely used in shut-off or on/off applications. In some valve terminology, gate valves are also referred to as globe valves.
kuitenkin, gate valves may not be the best choice for regulating flow or operating in any direction other than fully open or fully closed. Using partially open gate valves for throttling or flow control can lead to damage to the gate or valve seat ring due to collisions in the turbulent flow environment created when partially open.
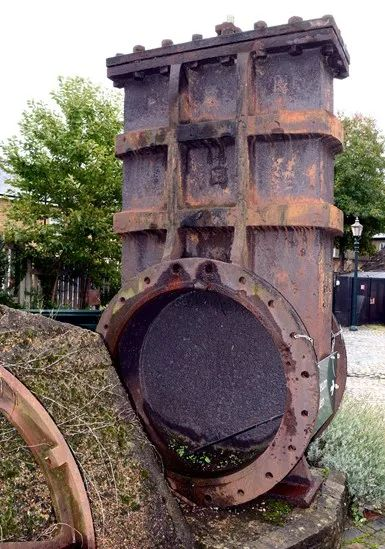
Gate Valve Internals structures
While most gate valves may appear similar in appearance, their internal designs can vary. Most gate valves consist of a body and bonnet, with the bonnet containing a closure element called a gate or disc. The closing element is connected to the stem passing through the bonnet, ultimately connected to a handwheel or other driving device for stem operation. The pressure around the stem is confined by packing compressed into the stuffing box or chamber.
Gate valve internals, unrelated to the thinness or fit of the valve, refer to components within the valve that endure significant stress or are subjected to severe erosion and corrosion. In gate valves, the internals consist of the stem, disc seat area, body seat, and back seat. Common bronze or brass valves typically have internals made of the same material as the body and bonnet. Cast iron and ductile iron valves use either all-iron internals or bronze internals.
Steel valves can be equipped with various internals materials, including tungsten chromium cobalt alloy, Hastelloy alloy, 316ss, 347ss, Monel alloy, and Alloy 20, commonly used for gate valve internals.
Gate Valve Disc Design
The core of gate valves is the closure element, which comes in two designs: wedge and parallel disc seat. The wedge design, popular since its invention by the British engineer James Nasmyth in 1843, utilizes a gate with a slightly inclined angle that matches the angle of the body seat for a tight closure. Wedge valves secure the gate firmly into the seat by applying torque.
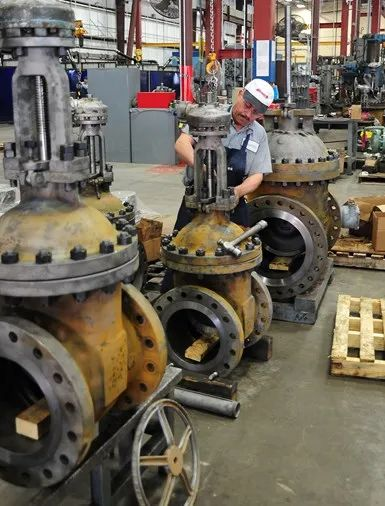
There are three types of wedge gate design:
- Solid wedge, the oldest and historically prevalent, was nearly universal at one point. kuitenkin, it lacks flexibility and may jam in the seat due to extreme temperature fluctuations or pipe stresses causing deformation. Solid wedge gates remain standard configurations for bronze, valurauta, water supply, and compact carbon steel valves (API 602 type).
- Fully flexible wedge is extremely flexible, adapting to temperature changes and adverse pipe stresses without constraint by adding grooves or slots around its periphery. Flexible designs are easier to manufacture, compensating for minor imperfections in the seat surface with the gate’s flexibility. To date, flexible wedge designs are the most common type on industrial gate valves.
- Split wedge consists of a two-piece design, with matching faces on the back of each gate. These matching faces allow even transfer of downward stem thrust to the gate surface and seat. This flexible design also prevents interference caused by thermal expansion. kuitenkin, split designs have a downside: in dirty applications, residue or debris may lump between the halves, causing misalignment or even blockage. Split wedge designs are common in stainless steel and high-alloy valves, as well as many small bronze valves.
Wedge gates are guided by grooves or ribs cast or welded to the valve body and directed by the seat. These wedge guiding devices maintain alignment during opening or closing, preventing sliding on the downstream seat during these processes.
Another valve disc style for gate valves is the parallel disc seat design. Parallel seats can install springs for a tighter seal or form a reliable seal in the upstream direction. Parallel seat is a positional seat; the gate’s position determines the sealing effect, rather than the magnitude of the force (torque) applied by the stem on the gate.
Body/Bonnet Design
Gate valves typically consist of two main parts: the body and the bonnet, forming the pressure-containing shell of the gate valve. There are various designs for the interface between these two components.
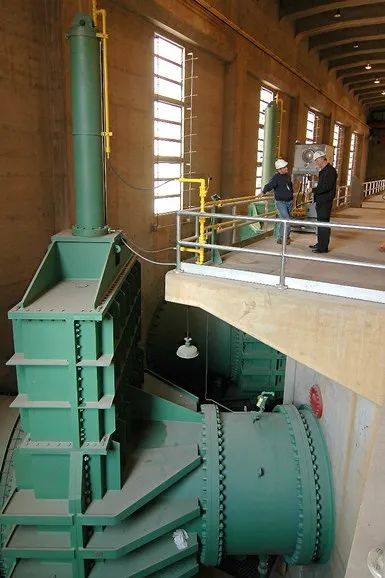
- Threaded joints are the simplest design but are only used for inexpensive, low-pressure bronze valves.
- Union joints are also mainly used for bronze valves, but the union design allows for easier disassembly, facilitating maintenance and repair.
- Bolted bonnet joints are the most popular joints, used for the vast majority of gate valves in today’s industrial applications. Unlike threaded and union bonnets, bolted bonnet connections require gaskets to seal the joint between the body and bonnet.
- Pressure seal joints are activated by fluid pressure inside the valve body acting on a wedge made of soft iron or graphite inserted between the body and bonnet. In pressure seal valves, the higher the pressure in the body cavity, the greater the force on the gasket. Pressure seal bonnets are widely used in high-pressure, high-temperature applications, such as in the power industry.
- Welded bonnet joints are a highly popular body/bonnet joint for compact steel valves ranging in size from ½ inch to 2 inches and pressure ratings from 800 kohtaan 2500, requiring no disassembly.
Materials and Standards
Steel and iron are the most commonly used materials in gate valve construction. Steel materials are suitable for most industrial applications, while iron materials are suitable for applications such as water, wastewater, and heating, ilmanvaihto, ja ilmastointi (LVI). Other commonly used gate valve construction materials include stainless steel, bronze, and high-alloy materials such as Hastelloy and chromium-nickel-iron alloys.
Concerning gate valve design and construction standards, domestic standards include national standards GB and GB/T, as well as industry standards JB and JB/T, along with group standards and enterprise standards. Internationally, standards are established by organizations such as the American Petroleum Institute (API), the Manufacturers Standardization Society (MSS), the American Water Works Association (AWWA), and the American Society of Mechanical Engineers (KUTEN MINÄ).
Gate Valve Submarkets
Although quarter-turn valves have taken a significant share of the gate valve market over the past 50 vuotta, some industries still heavily rely on gate valves, including the petroleum and natural gas industries. Despite advancements of ball valves in natural gas pipelines, crude oil or liquid pipelines remain the stronghold of parallel seat gate valves. In larger-sized valves, gate valves continue to be the primary choice for most applications, including the refining industry. Stability in design and economic total cost are crucial factors influencing the adoption of these valves.
In terms of application, many process industries use temperatures higher than the safe working temperature of polytetrafluoroethylene (PTFE), the main seat material for floating ball valves. High-performance butterfly valves and metal-seated ball valves have gained more usage in refining applications, although their total costs are typically higher than gate valves. In the water utilities sector, iron gate valves still dominate, proving cost-effective and durable even in buried applications.
The power industry employs alloy gate valves for applications involving extremely high pressure and temperature. Despite the emergence of some new Y-pattern globe valves and metal-seated ball valves designed for throttling services, gate valves continue to be favored in the utility sector.
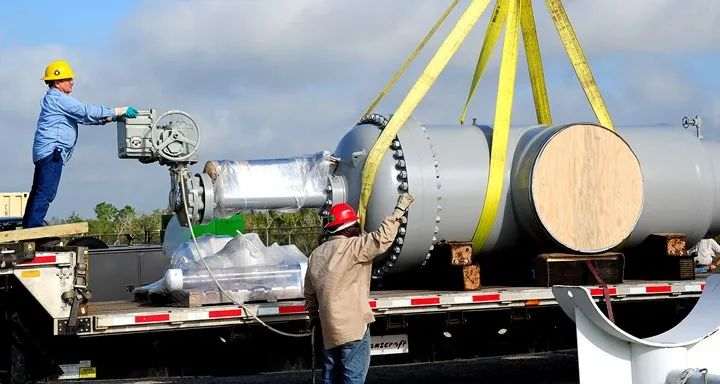
Tänään, luistiventtiilit, known for their high cost-effectiveness, remain the primary choice for many service applications. Mark Twain once said, “The reports of my death are greatly exaggerated.” While ball valves, tulppaventtiilit, and butterfly valves have expanded their market share over the decades, the longstanding gate valve is no exception to Twain’s sentiment – rumors of its demise have been greatly exaggerated!